Bilder
FAQs ClimaCheck

ClimaCheck
How do I troubleshoot if I get strange results?
If you experience unexpected or unrealistic data it is important to methodically check data and possible sources of error. All analysing of performance will regardless of method depend on both the accuracy of input and the use of proper calculations. The calculations is in the case of ClimaCheck defined by the used template and there are different templates for different applications. With ClimaCheck you can use the following troubleshooting method if you experience a deviation from expected or references values.
- Check measurement by measurement that each value is realistic. The best way to do this is obviously with a second meter if you have a specific issue but there are several means of identifying issues by looking at the measurements.
- Pressure sensors are typically quite linear with the most common error affecting offset. This means that it is often enough to checked versus atmosphere pressure but comparing with a traceable reference is always best.
- At stand still the pressure normally equalise if there is no solenoid. If both pressure sensors show the same you can almost be certain the measurements are good as it is a low likelihood two sensors with different ranges should show the same. You can also run pump/fans and stop compressor pressure should then equalise with the temperature of incoming air/water.
- It is normally also know what pressure is expected at a given exiting air/water temp of evaporator/condenser. Small deviations of pressure measurements has a low impact on performance and large should be identified by strange pressure readings.
- Temperature sensors/measurements with ClimaCheck is done with high accuracy Pt1000 class A sensors these can best be checked versus a known traceable reference.
- If you run the system with some flash gas at the sight glass the sub cool should be near zero.
- Power measurement most often creating “problems”. There are many computations with 3-phase power measurements and it is more seldom alternative measurement equipment with high accuracy is available.
- The easiest way to check is to compare power with compressor manufacturer data (the leading manufacturers often have softwares with reliable data whereas some offer less reliable data. It is important if you want to have high accuracy to be aware of that inaccuracy increase if you are below 20% of range of current transformers.
- You can check the power with a multimeter Volt/Amp measurement together with an assumption of 0.8-0.85 as normal power factor if you do not have detailed info. But this is more of an estimate.
- The only assumption the ClimaCheck method use is the energy balance over the compressor and the 93% will be a good assumption for heat losses for hermetic and semi hermetic compressors (the maximum identified in a survey was 10% and minimum 3% e.g. the error will be maximum 3-4% at extreme cases). This is only true if there is no additional cooling e.g. heat exchange with ambient air in a cabinet/room or external cooling through special devices such as oil or water cooling. External cooling can be:
- Liquid carry over from evaporator. This will give a warning for low superheat but also give a fictive high compressor efficiency (also gives warning) and fictive high COP/Capacity. Very few if any compressor manufacturers accept liquid carry over as this will drastically affect compressor lubrication as the liquid carry over will increase the refrigerant content of the oil which decrease the viscosity that result in increased wear and shortened lifetime expectance. Liquid carry over is a common problem on air to air and air to water heat pumps that are often originally designed for.
- Air cooling; if forced air is blown over the compressor the heat losses will increase in particular if the air is cold. This can be the case on condensing and low temperature semi hermetic compressors with fans to cool cylinder head. This can be handled:
- By shielding the compressor from the forced air flow if the pressure ratio is not so high that extra cooling is required or by shutting of the fan if the conditions allow this e.g. if the discharge is monitored to stay within allowable limits. Shielding is often easily done with a sheet of insulation or cardboard or similar. There is no requirement to make it tight just to remove the forced air as this increase the heat losses drastically.
- By adjusting the heat losses in the constant sheet. To identify what heat loss to use there are several means either experience can be used or comparison with the what is the measurement if the system can be monitored under known condition without fan.
- Oil/water cooling. This is common on larger compressor in particular in the industry and require additional measurements and special templates for calculations see special information on this.
- Liquid injection. To inject liquid injection can extend envelope of a compressor but as it decrease efficiency to inject liquid refrigerant it should only be used when necessary e.g. extreme conditions. This is often controlled by discharge or motor temperature. These systems require special calculations and accuracy can be significantly affected if effect of liquid injection is not known and taken into account.
I´m about to measure a chiller with a subcooler. What do I need to have with me on site?
Go to www.climacheck.com and go to ”Flowcharts and Templates”. Here you will find required equipment for most different units. In the case of a sub-cooler, you will need a template, 8 temperature sensors, 2 pressure transmitters and a power meter.
Do I need to measure the temperature between the hot gas heat exchanger and the condenser?
No, not unless you are interested in the hot gas heat exchanger capacity separately. Standard measurement with temperature measurements on hot gas pipe and after the condenser will give the total rejected heat with accurate COP. If measured with a separate sensor between the hot gas heat exchanger and condenser connected to the variable TT_Cond_in, software will show condenser capacity plus hot gas heat exchanger capacity. If you add water temperatures in and out from the heat exchanger you must use an optional module for four temperatures (RTD04) available for both field – and fixed measurement.
I have two compressors in the same refrigerant circuit. How do I do?
Normally, you measure joint hot gas temperature and power input to both the compressors when there is only one refrigerant circuit. Compressor efficiency is obtained for both compressors. By using a temperature sensor (normally TT_8) on one of the compressors it is easy to check that both of the compressors have the same temperature.
Compressor efficiency is 95%, it seems high?
If the compressor efficiency is unreasonably high, it is because errors in the measurement or if the compressor has an active cooling. Active cooling can be a fan, water or oil cooling or liquid injection. It may also be a result of liquid refrigerant in the suction line of which boils and cools the compressor. For stable operation and without cooling, compressor efficiency for the most efficient compressors have a compressor efficiency of appr. 75%.
Do I need to measure flow on the secondary side to get the COP?
No, the ClimaCheck method gives COP, heating – and cooling capacity, Compressor Efficiency etc without any flow measurement. By using the temperature and pressure measurements, most cooling processes using thermodynamic data for refrigerants and energy laws are analysed.
I have a portable device. Can I measure and analyse all types of plants?
In principle, any system can be measured but for complex systems this normally requires additional sensors and specialized information. As standard you can measure a lot of different plants. For example, a circuit with the condenser, heat exchanger or suction gas heat exchanger changer. PC-templates for these units are included as standard ClimaCheck portable devices but sent upon request to ensure that the correct model is used for different systems. Units with two circuits require more sensors. To see what accessories you need for a given circuit, go to ”Templates & Flowcharts”.
Does ClimaCheck work on transcritical CO2 systems?
Absolutely. We have extensive experience in measuring transcritical units and supplies for new construction and field measurements in particular the retail market since 2009. The measurements are of great help in such commissioning and troubleshooting. Contact us for more information.
Where I can find the manuals?
Manuals are installed together with the software during a special help and libraries, and many can be downloaded on the website. Before the start of measurement, it is important that you have the correct template and the right equipment. Many can be downloaded from the website under “Documentation and FAQs”.
What are the benefits with ClimaCheck Online?
With ClimaCheck online you can from any Internet browser to go in and analyse your plant. ClimaCheck sends data over the Internet to our server where the analysis is done. Therefore, no software is required. In ClimaCheck Online, energy statistics and reports are included. Here, the plant owners can easily see how much energy the plant uses and there are also features that reflects historical energy consumption which gives a good indication of how the system is optimized.
I measure the electrical input of a residential heat pump and I believe the value is not correct
The current clamps supplied with portable equipment have a measurement error of up to 3% in the range 20-100 A. Below 20 A, the accuracy is poor, and we recommend to use fixed current transformers instead. With an input power of 3 kW electrical output of the measurement error can be above 10%, which affects the cooling- and heating capacity with the same error, while the COP value is not affected.
Is it possible to monitor different equipment from the same client, located at the same place at the same time, using single ClimaCheck equipment?
Each ClimaCheck central unit “PA Pro” has 8 pressures and 8 temperatures on board and can be expanded with additional modules most common is the RTD04 with 4 temp. These are connected to the central unit with a “telephone cable” so they are easy to extend to get x*4 temp at some distance. This said wiring is expensive so distances put some limits on cost effectiveness. If you have two chillers close to each other it is clear you normally would connect these to one PA Pro. If they would be 50-100 m apart you would typically use 2 PA Pro. If you look at the pricing you will see that the PA Pro central unit is quite cost effective versus the expansion units. Then when it comes to communication over modem there are two ways either RS232 modems for single PA Pros or Router modems for LAN with multiple PA Pros there is an added cost to the Router modem but for several PA Pros it is clearly much cheaper. The result is that there can be a cost effectiveness to expand the first PA Pro but if you move to two PA Pros then there is less cost advantage. Each PA Pro can handle maximum 100 analogue “channels” where maximum 50 can be on bus communication. Both the ClimaCheck software and ClimaCheck Online can be set up to take data from one Source and split and present it to several analyses.
FAQs didn’t solve your problem?
Fri3Oil System Distributors
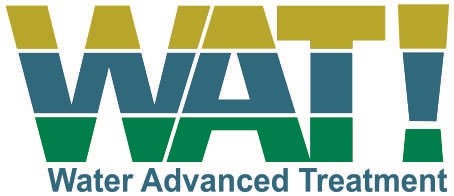
Fri3Oil System WAT!
International Distributors Worldwide
Where you can find them:

Europe
Aichham 11, 4650
Lambach, AUSTRIA
Tel. +43724532341
Email. office@agatex.at
Web. www.agatex.at
Atomitie 1
00370 Helsinki, FINLAND
Keskus +358 9 5657 780
Suora +358 9 5657 7813
Email. info@refair.fi
Web. http://www.refair.fi/
Domonique Gagnepain
Tel. 0033 682 134 920
Web. france@refriapp.es
17 Miliaraki str
111 45 Athens, GREECE
Tel. +30210 2280384 -2286268
Fax. +30210 2286912
Email. george@soldatos.gr
Web. http://www.soldatos.gr
KÜHL ANALYSE
An der Brauerei, 73
08412 Werdau OT: Steinpleis.
Germany.
Email. info@Kuehlanalyse.de
Web. http://kuehlanalyse.de/
LINHATOTAL, GESTÃO E REPRESENTAÇÕES AVAC LDA.
R Juiz Margarido Pacheco,27
Canelas
4410-310 Vila Nova Gaia – Portugal
www.linhatotal.com
Telf: +351911572243
geral@linhatotal.com
Dragoon House, Westside View, Waterlooville
PO7 7SF, UNITED KINGDOM
Tel. +44 23 9223 0007
Email. info@businessedgeltd.co.uk
Web. www.businessedgeltd.co.uk/
Alunișului 164, Sector 4, București, 040747, ROMANIA
Móvil. 0040721431904
Tel/Fax. 0040213320848
Email. office@abtehnic.ro
Web. http://www.abtehnic.ro/
Rest of the World
Rodolfo N. Scheiner
Tel. +543424891062
Email. rodolfo@refrigeracionmr.com.ar
P.O.Box 8047, 3 Ha Omanut Street
Netanya 42180, ISRAEL
Tel. +972 9 8654101
Fax. +972 9 8659111
Email. info@supco.co.il
Web. http://www.supco.co.il/
Oficina Bogotá
Pasadena Cra 53 N° 102-48
Bogotá, COLOMBIA
Telefax. (1) 5331391 – 6162477
Celular. 315 753 4804
Email. nuevastecnologias@friocostasa.com
Web. http://www.friocostasa.com/
Unit 3, Lot 22 Dell Road, West Gosford NSW 2250 AUSTRALIA
Tel. +61 2 4322 8448
Móvil. 0424 844 425
Fax. +61 2 4324 9791
Email. service@mmtechnical.com.au
Web. www.mmtechnical.com.au
Do you want to be our Official Fri3Oil System WAT! Distributor?
FAQs F3OS
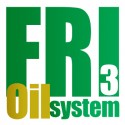
Fri3Oil System
Is the System able to recover and recycle all refrigerants?
Fri3Oil System can recover and recycle on site all halocarbon refrigerants: CFC’s, HCFC’s y HFC’s.
After one cleaning, is it posible to reuse the old recycled refrigerant with Fri3Oil System?
Refrigerants, once recovered and recycled, have a minimum quantity of impurities: less than 600ppm in the worst of cases. This quality makes them ideal for their reuse, with a total security that they will not damage the equipment in which they are introduced.
Is it posible to extract WATER from a plant in which, for example a heat exchanger has been communicated, and it is flooded in water?
The cleaning of water is one of the most difficult(I´d rather say complex) practices we can do with Fri3Oil System, due to the problems of ice blockages that can be created in key points like: the dryer at the entrance of the main machine, or in the expansion valve.
However, and through a proccess which is perfectly explained in our training DVD, it is possible to extract until the last drop of water from any plant, saving this way these equipments that, otherwise would be disposed.
I have to RETROFIT from MO to POE, can Fri3Oil System help me in this task?
As we mentioned, it is a cleaning system for refrigerated circuits, that can also recover and recycle any halocarbon refrigerant at the samen time.
This means that, once we have recovered all the HCFC refrigerant from a plant, we will have reclyced it all and separated it from the MO that used to contain.
Therefore, if we proceed to the cleaning of the interior of the circuit, we will assure the total extraction of the installation MO content, avoiding this way, a phase separation by an excess of MO and its mixure with POE. The HCFC would be kept and recycled, bieng idela for maintenance services until end of 2014.
Could the system be used to clean up recovered refrigerant which has been taken out of a plant and stored in a recovery cylinder?
YES, of course, and not only it can be recycled and reused without problems, but also that cylinder that stores the gas can be cleaned as well.
About the REA,what is it exactly, and what are its functions?
The REA is an 7,1ltr capacity External Oil Recipient, that mainly has 3 funcitons:
- Permanent REA: It is connected to the main machine on each cleaning. Its mission is to house all the dirt from the circuit interior: Oliz, acids, water, etc.
- Intermediate REA: This REA is placed between the Fri3Oil System main machine and a circuit in which, predictably/likely there is water. Its objective is to receive the major part of this water, in order to avoid it entering the machine and create obstruction problems. For further information, please consult our Training DVD.
- POE oils Handling: One of the principal uses of the REA by our clients is the handling of POE oils. It is used to store the spare oil. Once in the REA, it is pressurized by the refrigerant we cose, in order to sep it untl it use, avoiding its damage by air exposition. For further information, please read the Artícle 15, The REA, uses and applications.
In which installations can it be applied?
Fri3Oil System is valid for ALL installations containing halocarbon refrigerants, independently of its size.
For Information about special installations cleaning due to their big size, please consult clients/users FAQ´s section in our website, or our Training DVD.
I have recovered and recycled with Fri3Oil System 150kg of R-134a refrigerant from a plant, from which I have extracted 6 ltr. Of contaminated oil. What do i have to do with this contaminated oil? Should I throw it away? Can it be recycled? Who is in charge of that?
All this dirt is sent in a non-hermetically-sealed recipient to a waste dealer, like any oil coming from a recovery. The waste dealer will incinerate these products.
How do you know that the refrigerant has been cleaned to an adequate standard?
The System has been tested many times in lab and it always achieved a less than 200ppm result of impurities in the recycled refrigerant, in the worst of the cases.
What is an acceptable European Standard for the quality of refrigerant (Moisture Content (ppm), Particulates, Blend % Corruption, etc.
There are no fixed regulations about it, except ARI720 which affects to virgin product, and not recycled one.
Regarding the blends, there are only some doubts concerning those high glide products, like R-407C, that should be analized in case of doubt. In the practice, what professionals do is to recover this refrigerant in quantities of 1tn in a recipient, which is later sent to the waste dealer. The waste dealer, with the authorisation of the “patenter” will “re-compose” the product.
For the rest of the blends with low glide, no comprobation is needed. The performance of the product, and its vapur tension is very similar to the original one.
Does the Fri3Oil Machine Empty / Self-Evacuate itself thoroughly and to what level in order to avoid cross contamination when working with different refrigerants?
The Fri3Oil System main machine does not self-evacuate. It is necessary” an ordinary recovery machine, by communicating the high-low pressure, opnening the by-pass valve asd through the oil take, and valve 10 it is possible to extract all the oil remaining in the unit, except a few ppm that can remain inside the oil in the main mahcine compressor carter.
Is the FriOil Machine safe for use with Hydrocarbon Refrigerants?
Eventhough, inside the controller program, it is possible to find these refrigerants, and, technically it is viable, we decided to remove them, as they would not pass an explosion proof.
How is Oil Contamination between the System Oil and the Fri3Oil System Compressor Oil avoided?
It is not posible to do more of what physically the liquid separator does.
Nevertheless, there are little particles that pass with the refrigerant vapour to the compressor carter. For this reason, we recomend, not only to replace the oil when needed, but also to change it each 200working hours, as a preventitive measure, in order to get a better lubricity of the oil and compressor.
How can I clean the REA Fri3Oil System Vessels for future re-use?
The REA must be cleaned with the same principles that we use for any equipment, and that can be learned in the training course.
In the practice, refrigerant is injected through the liquid valve, sucking by the vapour one, and having placed the REA upside down. For the final recovery of the remaining refrigerant which there is from the vapour valve to the bottom, the REA must be tilted, in order to leave in the lowest point the vapour valve.
What UK companies will accept refrigerant recovered via the FriOil System which is sent to them for destruction? (The REA has to be returned or you must transfer to normal recovery Cylinder? This requires another Recovery Machine which in turn might become contaminated)
This question is answered in question no. 8
FAQs didn’t solve your problem?
Mediathek
RefriApp Multimedia
Kontakt
Haben Sie eine Frage? Setzen Sie sich mit uns in Kontakt!
Wir werden versuchen Ihnen innerhalb der nächsten 24 Stunden zu antworten
Wo Sie uns finden können
Unser Betrieb befindet sich in der andalusischen Provinz Almería im Südosten Spaniens
Ueber Refriapp

RefriApp

Über unsere Aktivitäten
Wir bieten eine Reihe spezieller Werkzeuge:
- Zur Erfüllung der gültigen Gesetzgebung bezüglich der Kontrolle von Leckagen fluorierter Kältemittel; zur Umrüstung von Anlagen von HFCKWs auf fluorierte Kältemittel; für Inbetriebnahmen, Inspektionen und Energiezertifikationen.
- Zur Ausstattung des Kältefachmannes mit effizientem Arbeitsgerät.
Unsere Geschichte
RefriApp übernahm das Know-How aus mehr als 40 Jahren Erfahrung im Kältesektor, im Speziellen 23 Jahre im Bereich der Kältemittel, Schmieröle und der Reinigung von Kältekreisen.
Unser Team
Unser Team bildet sich aus jungen Kältefachmännern und -frauen, die bereits weitreichende Erfahrungen im Kältebereich sammeln konnten.
Kontinuierliche Expansion um den Globus

RefriApp kooperiert mit Kunden in weltweit über 30 Ländern.
Des Weiteren arbeiten wir zur Zeit mit qualifizierten Vertriebspartnern zusammen, die unsere Dienstleistungen und Produkte in 20 Ländern in Europa, Südamerika, Nordamerika, Afrika, Asien und Ozeanien anbieten.

Unser Betrieb
Halle mit 500 Quadratmetern zur Fertigung, Reparatur und Wartung, der von uns vertriebenen Produkte.
Zusätzlich verfügen wir über eine Versuchskälteanlage zur Kalibrierung und Validierung unserer Geräte sowie für Schulungen von internem und externem Personal.
In unserem Multimedia-Raum führen wir unseren Schulungen durch, sowie kommerzielle Präsentationen, Vorträge und Debatten professioneller Kältetechniker wie in unserem internationalen Meeting “The Fri3Oil System family“.
Des Weiteren wird der Raum zur Vorführung unserer Sonderanwendungen der Kälte- und Klimatechnik genutzt.
Unsere Büroräume bestehen aus den Arbeitsräumen unserer Ingenieure, dem Bereich der Geschäftsführung, sowie einem zusätzlichen Meeting-Raum.
Startseite
Willkommen bei RefriApp
Schulungen bei RefriApp
Multimedia
Kontinuierliche internationale Expansion


Aktuelle Neuigkeiten
Fri3Oil System evolve to WAT! Water Advance Treatment. Unveil at Chillventa 2016.
RefriApp is proud to announce the worldwide release of WAT! its band new HVAC cleaning system WAT! Water Advance Treatment at Chillventa, Nuremberg, stand 8/8-207. This new model is a evolution of the successfull Fri3Oil System V.E.A.3, keeping strong points, with a wide range of improvements forward an easier, more intuitive and more automatic use. […] Continue Reading
RefriApp launches its Corporate Brochure
RefriApp launched its corporate brochure which will be used to illustrate the different facets of this young company that manufactures and distributes special applications for maintenance of HVAC and Refrigeration installations worldwide. The brochure showcases corporate philosophy and its commitment with innovation, technological development and international expansion, in addition to a detailed review of its different technological solutions (cleaning, […] Continue Reading
Professionelle Meinungen zu unseren Produkten





